
Commercial Loading Dock Repair in La Mirada, Los Angeles, and Orange County
Commercial dock repair helps maintain safe and efficient loading and unloading operations. Over time, docks experience wear and tear, including damage to bumpers, dock levelers, and seals. Professional dock repair services begin with a thorough inspection to identify structural damage, misalignment, and equipment malfunction. Skilled technicians then perform necessary repairs, including replacing damaged parts, welding cracks, and adjusting the levelers for optimal performance.
-
All components in good working order prevent accidents and operational delays. Maintenance and timely repairs of commercial docks extend their lifespan and improve safety and productivity in logistics and distribution. Keeping docks in optimal condition is essential for smooth and efficient business operations, minimizing downtime, and enhancing the overall functionality of the facility. This service is vital for businesses that rely on robust and reliable docking systems for their daily operations.
We Repair
-
Levelers
Properly functioning levelers are essential for smooth loading and unloading operations. Maintenance and repair services address misalignment, wear and tear, and hydraulic problems, ensuring efficient and safe dock operations.
-
Bumpers
Dock bumpers protect the dock and vehicles from damage during loading and unloading. Repair services include replacing worn or damaged bumpers, which helps prevent costly damage to the dock and trucks and maintains safety and efficiency.
-
Seals/Shelter
Dock seals and shelters are vital for maintaining a controlled environment within the facility. Repair services fix issues like rips, tears, and general wear, helping to keep out weather, pests, and contaminants, thus improving energy efficiency and product safety.
-
Truck Restraints
Truck restraints are crucial for securing vehicles during loading and unloading to prevent accidental movement. Repair services ensure these systems function correctly, address mechanical issues, and maintain the safety of personnel and equipment.
-
Gates
Gates provide security and controlled access to the dock area. Repair services for gates include fixing mechanical failures, alignment issues, and damage, ensuring the gates operate smoothly, and providing the necessary security.
-
Other Equipment
Additional dock equipment, such as lights, dock plates, and ramps, are essential for safe and efficient dock operations. Repair services cover a broad spectrum of issues, ensuring all equipment functions correctly and supports smooth dock activities.
Signs a loading dock needs repair
-
Cracks, dents, or other visible damage on the loading dock surface or structure indicate that repairs are needed. These issues may weaken the dock’s structural integrity and safety; addressing them promptly prevents further deterioration.
-
Difficulty operating dock equipment, such as levelers, bumpers, or truck restraints, suggests that the dock may require repair. Malfunctioning equipment can lead to inefficiencies and pose safety risks during loading and unloading processes.
-
Noises like grinding, squeaking, or clanging during dock operations can indicate mechanical problems. These noises often signal wear and tear on moving parts, which may need immediate attention to avoid more significant issues.
-
Signs of water damage, such as rust, mold, or rot, on the dock or its equipment indicate that repairs are necessary. Water damage can weaken the structure and lead to unsafe conditions, requiring prompt action to restore the dock’s integrity.
-
If dock levelers or doors do not align correctly with trucks or loading areas, it can disrupt operations and pose safety hazards. Misalignment issues often require professional repair to restore proper function and alignment.
-
General wear and tear, such as worn-out seals, damaged shelters, or frayed cables, indicate that the loading dock needs maintenance and repair. Addressing these issues can improve its overall performance.
The Commercial Loading Dock Repair Process
Our Reviews
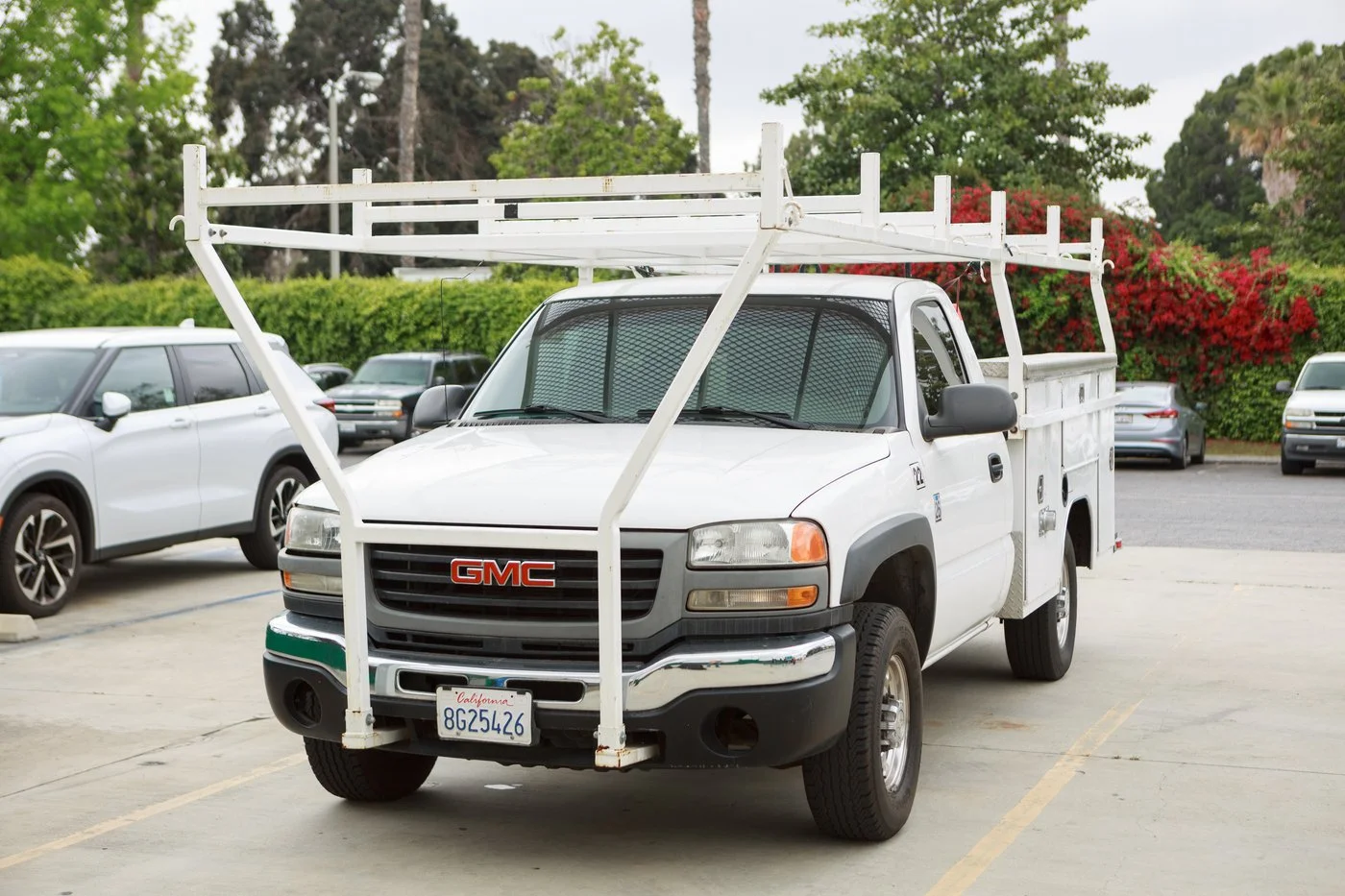
Our Service Area
Orange County, CA: Aliso Viejo, Anaheim, Brea, Buena Park, Costa Mesa, Cypress, Dana Point, Fountain Valley, Fullerton, Garden Grove, Huntington Beach, Irvine, La Habra, La Palma, Laguna Beach, Laguna Hills, Laguna Niguel, Laguna Woods, Lake Forest, Los Alamitos, Mission Viejo, Newport Beach, Orange, Placentia, Rancho Santa Margarita, San Clemente, San Juan Capistrano, Santa Ana, Seal Beach, Stanton, Tustin, Villa Park, Westminster, Yorba Linda
Things to Consider Before Repairing a Loading Dock
-
Professional assessment determines the full scope of loading dock deterioration. Our technical evaluation examines structural integrity, mechanical systems, and safety features. Comprehensive analysis reveals hidden damage that might affect repair effectiveness. This detailed inspection process supports accurate repair planning while preventing unexpected complications.
-
Our detailed financial analysis compares the long-term value of repairs against replacement options. Our professional evaluation considers future maintenance requirements and operational efficiency. The technical assessment includes energy efficiency improvements and modernization benefits. This comprehensive approach supports informed decisions about facility investments.
-
Strategic planning minimizes business disruption during dock repairs. Our scheduling process coordinates with facility operations to maintain productivity. Professional project management includes timeline optimization and resource allocation. This systematic approach reduces repair impact while maintaining quality standards.
-
Professional repairs maintain compliance with current safety regulations and industry standards. Our technical team stays current with evolving compliance requirements and safety protocols. Detailed documentation supports regulatory inspections and insurance requirements. This comprehensive approach protects businesses while maintaining safe operations.
Common problems with industrial and commercial docks
-
Surface damage
Industrial and commercial docks often experience surface damage, such as cracks, potholes, and erosion. These issues can result from heavy use, exposure to harsh weather conditions, and the constant movement of heavy equipment and vehicles. If not addressed promptly, surface damage can create safety hazards and disrupt operations.
-
Mechanical failures
Dock levelers, truck restraints, and other mechanical components are essential for the smooth operation of docks. Over time, components fail due to wear, lack of maintenance, or exposure to harsh conditions. Mechanical failures can lead to operational delays, increased repair costs, and safety risks.
-
Alignment issues
Misalignment of dock levelers, doors, or bumpers can cause significant operational inefficiencies. Alignment problems often result from improper installation, frequent use, or impact damage. Misaligned equipment can make it difficult to load and unload goods safely and efficiently.
-
Weather-related damage
Docks are exposed to various weather conditions, including rain, snow, and extreme temperatures. Weather-related damage, such as rust, corrosion, and water infiltration, jeopardizes the structural integrity of the dock and its equipment. This type of damage requires regular inspection and maintenance to prevent long-term issues.
-
Wear and tear
Continuous dock use leads to general wear on components, including seals, bumpers, and dock doors. Over time, these components may deteriorate, leading to reduced performance and increased maintenance needs. Inspections and replacement of worn parts are critical to maintaining dock functionality.
-
Electrical problems
Docks often rely on electrical systems to power equipment such as lighting, levelers, and security features. Electrical problems, such as faulty wiring, short circuits, or power surges, can disrupt dock operations and pose safety hazards. Maintenance and electrical issue repair are crucial for ensuring reliable dock operation.
-
Insufficient maintenance
A lack of regular maintenance can exacerbate the above issues. Without routine inspections and timely repairs, small problems can escalate, disrupting operations and requiring costly repairs. Implementation of a comprehensive maintenance plan increases the lifespan of industrial and commercial docks.
Call Now for Garage DOck Repair
Commercial customers in La Mirada, CA, and Orange County who need commercial dock repair should contact Prime Dock & Door LLC. We provide same-day service, quality craftsmanship, and professional results.
FAQ’S
-
Hydraulic failures, worn-out dock levelers, broken seals, damaged bumpers, and concrete deterioration.
-
At least twice a year or whenever performance issues arise.
-
Stop operations immediately and call a professional repair service to assess hydraulic or mechanical issues.
-
Minor repairs take a few hours, while complex issues may require 1–2 days.
-
Costs vary based on the extent of damage, typically ranging from $500 to $10,000.
-
We specialize in hydraulic system diagnostics, fluid refills, and component replacements.
-
It depends on your policy; some commercial property insurance plans cover damage repairs.
-
We offer modern upgrades, including energy-efficient seals, safety enhancements, and automation.
-
Yes, we offer 24/7 emergency loading dock repairs to minimize operational downtime.
-
Vehicle restraints, bumpers, dock seals, and automated sensors should be regularly inspected.
-
Implement a preventive maintenance plan with regular inspections and minor adjustments.
-
Yes, we repair rolling steel, sectional, and high-speed dock doors.
-
We provide complete loading dock replacement services with custom design options.
-
Contact us via phone, email, or online booking form to arrange a service appointment.
-
Professionals ensure OSHA compliance, proper diagnostics, and long-lasting solutions without safety risks.